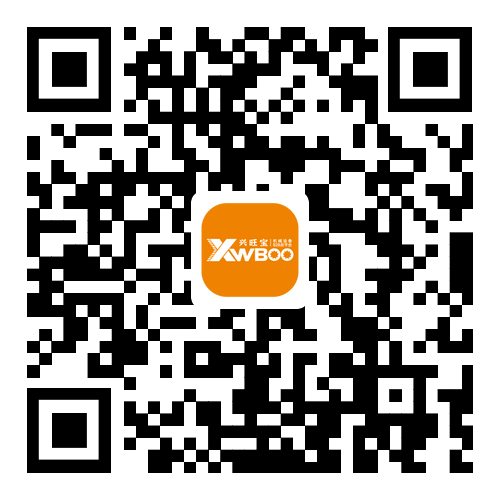
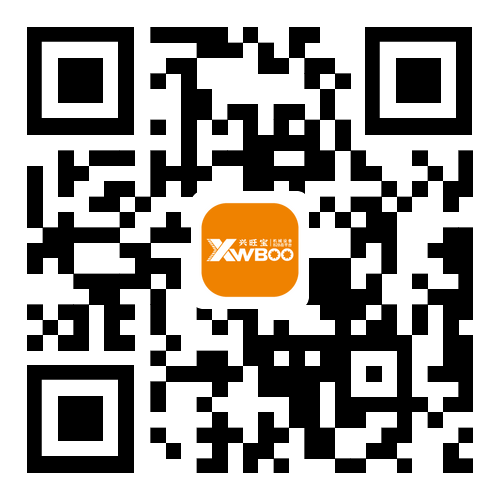
参考价 | 面议 |
产品详情
四轴和六轴工业机器人的保养方法涵盖了日常维护、保养周期和保养步骤等多个方面。这些保养措施旨在确保机器人的正常运行,并延长其使用寿命。以下是一些具体的保养建议:
一、日常维护
日常维护是确保工业机器人长期稳定运行的关键。操作人员应每天对机器人进行清洁和检查,包括清除灰尘、油污等杂质,并检查各部位是否有裂缝或损坏情形。此外,还需检查机器人的油封部位,预防油分的累积,以及在运转结束后开启排脂口、排油口,恢复内压。同时,通电后应检查机器人的振动、异常声音及电机发热情况,确认各轴平滑运动,电机的温度无异常增高。
二、保养周期
工业机器人的保养周期并非固定,而是根据机器人的使用频率、工作环境等因素来确定。一般来说,较为常见的保养周期为3个月或6个月。对于使用频率较高、工作环境较恶劣的机器人,建议每3个月进行一次保养。在保养周期内,应对机器人进行全面检查和维护,确保其处于工作状态。
三、保养步骤
保养步骤通常包括清洁、润滑、更换易损件等。清洁时,应特别注意冷却风扇和进风口/出风口的清洁,使用除尘刷和吸尘器进行清洁。润滑时,应选择合适的润滑剂,并按要求涂抹在各润滑点。对于易损件,如滤布、电池等,应根据其使用寿命及时更换。此外,还应对机器人的电气系统进行检查,确保电缆、传感器等部件的正常工作。
四、针对性保养建议
考虑到工业机器人的特殊性和需求,以下是一些针对性的保养建议:
综上所述,四轴和六轴工业机器人的保养方法需要综合考虑日常维护、保养周期和保养步骤等多个方面。通过实施这些保养措施,可以确保机器人的正常运行,延长其使用寿命,并提高生产效率。
The maintenance methods of four-axis and six-axis industrial robots cover many aspects such as daily maintenance, maintenance cycles and maintenance steps. These maintenance measures are designed to ensure the proper functioning of the robot and extend its service life. Here are some specific care recommendations:
1. Daily maintenance
Routine maintenance is the key to ensuring the long-term stable operation of industrial robots. The operator should clean and inspect the robot every day, including removing dust, oil and other impurities, and check whether there are cracks or damage in each part. In addition, it is necessary to check the oil seal of the robot to prevent the accumulation of oil, and open the fat discharge port and oil discharge port after operation to restore the internal pressure. At the same time, after powering on, the vibration, abnormal sound and motor heating of the robot should be checked to confirm the smooth movement of each axis and the temperature of the motor is not abnormally increased.
Second, the maintenance cycle
The maintenance cycle of industrial robots is not fixed, but is determined according to factors such as the frequency of use of the robot and the working environment. In general, the most common maintenance interval is 3 or 6 months. For robots that are used frequently and have a harsh working environment, it is recommended to maintain them every 3 months. During the maintenance interval, the robot should be thoroughly inspected and maintained to ensure that it is in optimal working condition.
3. Maintenance steps
Maintenance steps typically include cleaning, lubrication, replacement of wear parts, etc. When cleaning, special attention should be paid to the cleaning of the cooling fan and air inlet/outlet, using a dust brush and vacuum cleaner. When lubricating, the appropriate lubricant should be selected and applied to each lubrication point as required. For wearing parts, such as filter cloths, batteries, etc., they should be replaced in time according to their service life. In addition, the robot's electrical system should be checked to ensure that the cables, sensors, and other components are working properly.
Fourth, targeted maintenance suggestions
Considering the particularity and needs of industrial robots, the following are some targeted maintenance suggestions:
For robots used in high-temperature environments, the internal pressure of the grease and oil groove should be checked regularly to avoid poor lubrication caused by high temperatures.
For robots that often perform reversal actions, the inspection and maintenance of the motor and transmission system should be strengthened to prevent the occurrence of failures.
For robots used in wet environments, the robot body and surrounding environment should be dried regularly to prevent rust and corrosion.
When carrying out maintenance, you should refer to the operation manual of the robot and the manufacturer's recommendations to ensure the correctness and effectiveness of the maintenance work.
To sum up, the maintenance methods of four-axis and six-axis industrial robots need to comprehensively consider multiple aspects such as daily maintenance, maintenance cycle and maintenance steps. By implementing these maintenance measures, you can ensure the normal operation of the robot, extend its service life, and improve production efficiency.